In manufacturing companies very important factor is to optimally utilise manufacturing resources, timely execute orders and maintain high level of products quality. It is also necessary to register, settle and analyse all, also indirect, costs associated with production process.
ERP Managing production system
Comarch ERP XL provides comprehensive support in managing production processes (both mass and unit production). End products are manufactured according to precisely defined norms and technological standards, what results in reduction of product defects. In case of manufacturing products of a low quality, system user has possibility of fast identification of the faulty items directly in the system.
Important system functionalities, from the perspective of manufacturing company specificity
- Comprehensive support in managing production processes – with possibility to create technological cards describing specific production stages,
- Project scheduling (including availability of resources),
- Planning of production pipeline in a way, which allows to meet defined delivery dates,
- Simple interface to manage production, which can be operated via touch-screen devices,
- Managing entire path of documents typical for the manufacturing industry,
- Possibility of monitoring raw materials leftovers,
- Optimization of storing materials in the warehouse,
- Efficient project management, including project budgeting functionalities,
- Advanced search functionalities, e.g. allowing to identify suppliers of any raw material,
- Complex support of all enterprise departments, including logistics, HR, accounting, customer relationship.
Registration of production process
Expanded mechanism of settling production enables to associate costs from different sources to all manufacturing objects within multiple categories. Costs can associated based on various documents, e.g. sales document, accounting document, payroll, account balance or other cost objects. Apart from that it is possible to associate costs not having direct origin, e.g. additional margins. As a result any company can calculate real costs of manufacturing each of the products in very precise way.
BUSINESS INTELLIGENCE
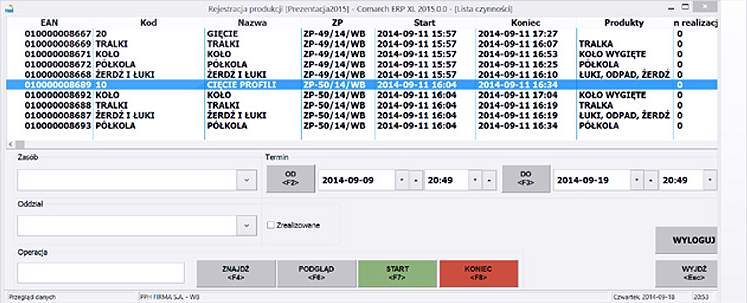
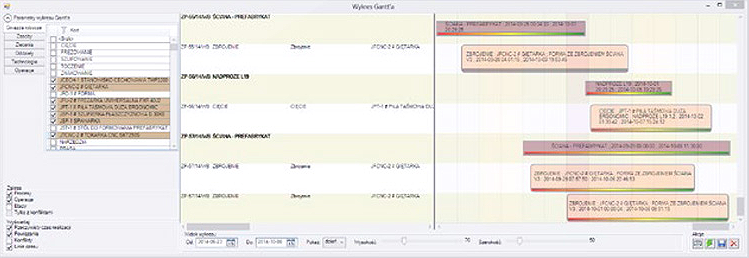